Extrusion et co-extrusion
At the heart of
our expertise
Progress Silicones presents two of its areas of expertise, useful for your requests and meeting your various specifications.
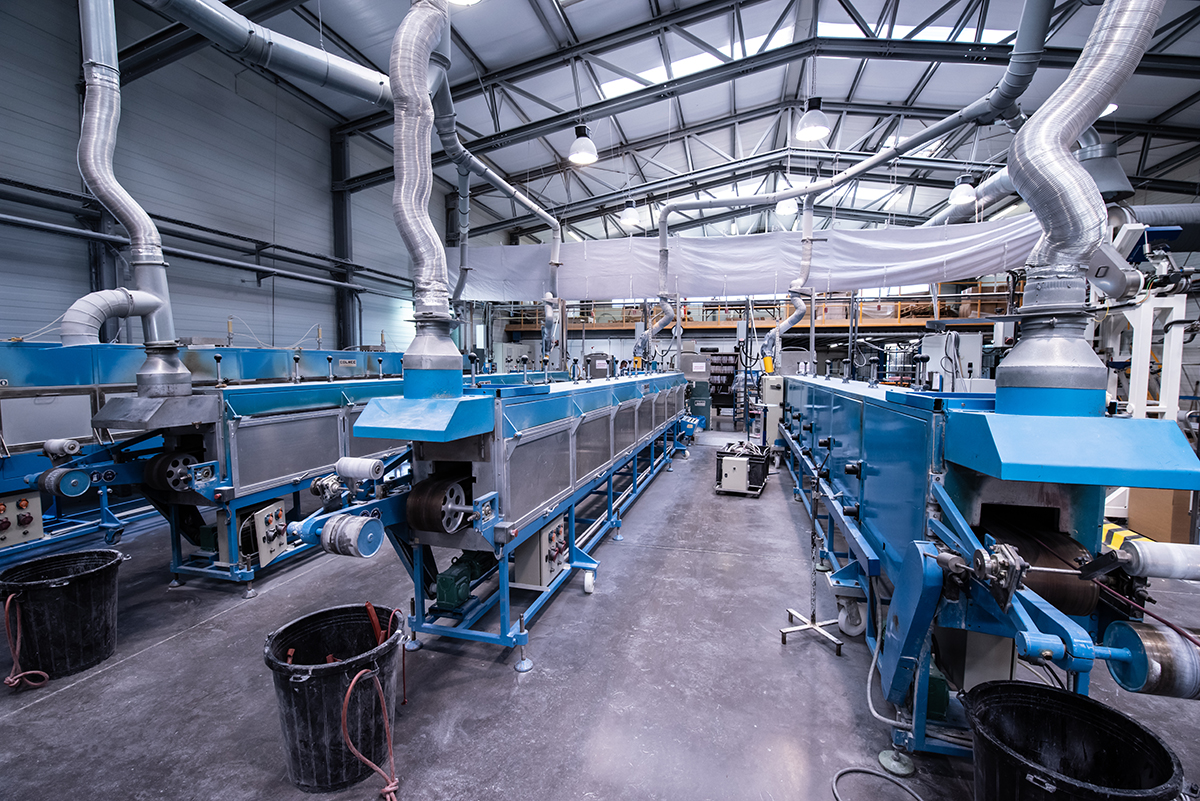
The extrusion technique
This extremely precise manufacturing process consists of bringing a silicone part into a die with the shape and size of the desired part as the final result. This mechanical process gives rise to parts close to perfection, requiring little or no machining a posteriori.
Progress Silicones has a wide range of exterior or interior shapes ranging from a few tenths to a few millimeters thick (more than 5000 die).
La technique
de la co-extrusion
Extrusion can give rise to different processes, including co-extrusion. It consists of an addition of two extruded products that will end up in one. A hollow O-ring can thus be filled or injected via the co-extrusion process.
The extruder will need an auxiliary system to achieve this performance. Two different products will be combined to give rise to a finished product composed of two materials.
But co-extrusion is not just a hollow part filling. It can also seal together two different materials to give a protective epidermis or varnish to the finished product.
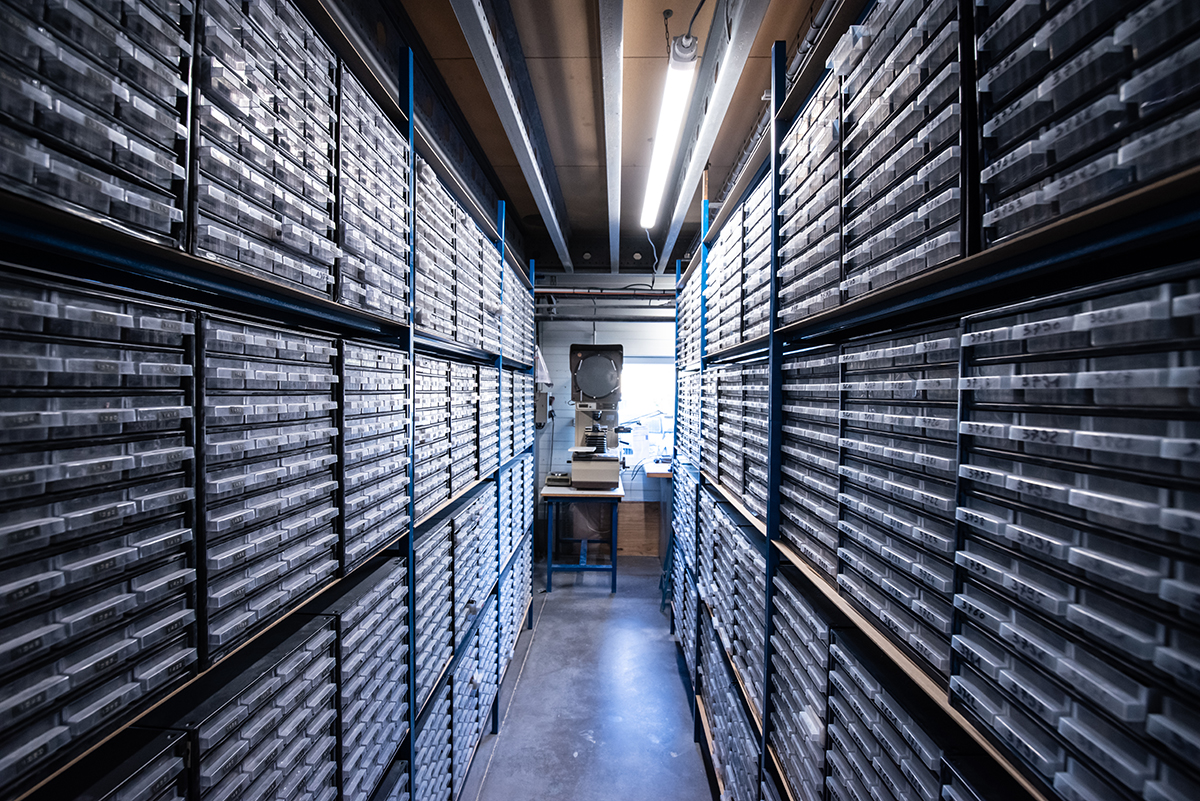
Progress Silicones' expertise:
extruded in compact gum or cellular
The added value of Progress Silicones lies in its expertise and experience as well as in a specific choice of materials. This is the case of the compact or cellular gum that makes it possible to make extruded or co-extruded parts of optimal quality.
Once the extrusion or co-extrusion process is complete and depending on the desired utility and shape, the parts supplied by Progress Silicones can be adapted to different areas. This can give, for example, an electrical insulation, a simple seal, a non-toxic seal for the food industry, a profile for the lighting industry...
Progress Silicones' compact or cellular gum products can also meet the needs of elite industries, such as nuclear (nuclear reactor seal) or the medical and pharmaceutical sector.
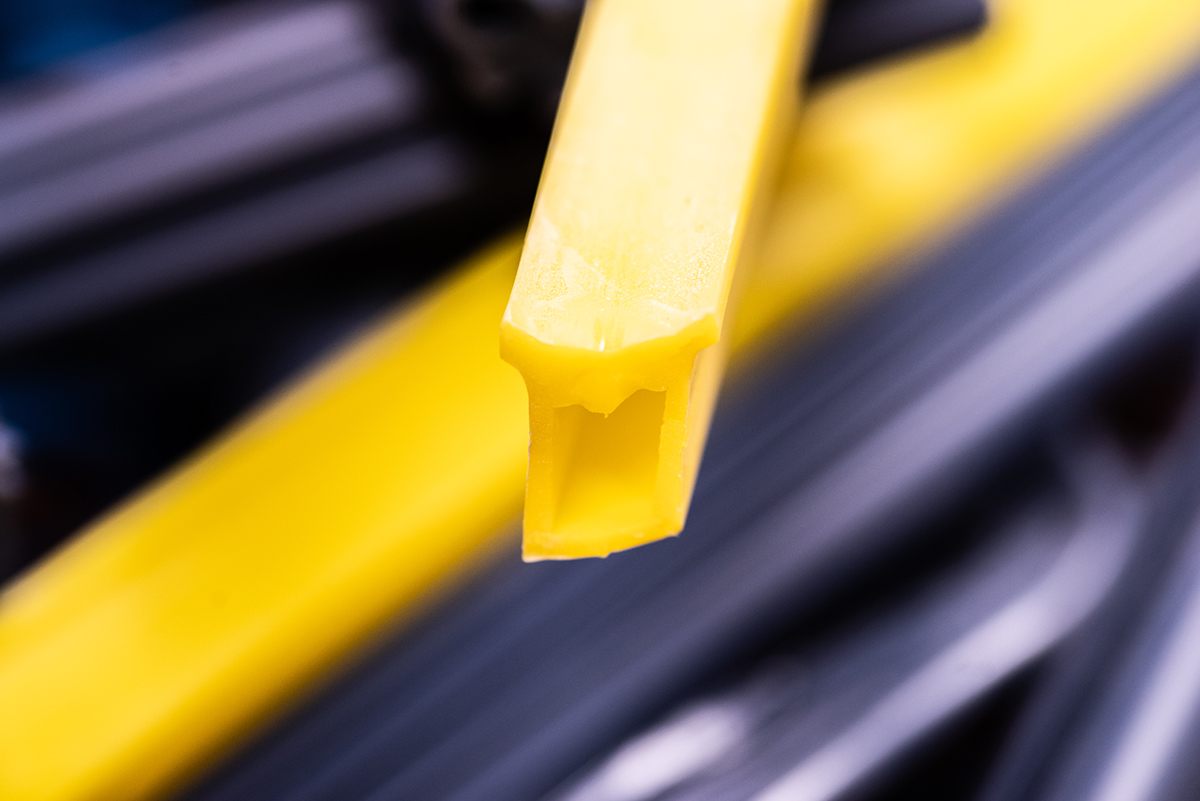
Our different extrusion techniques
Extrusion is extremely diverse and can adopt multiple geometric profiles. Progress Silicones offers different techniques to allow you to make the parts you need:
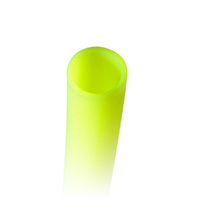
▼ Tubes: Extrusion of long custom products is possible thanks to our state-of-the-art equipment. Tubes or pipes are extruded for all your applications.
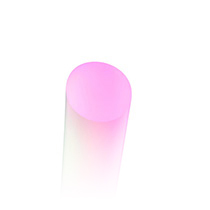
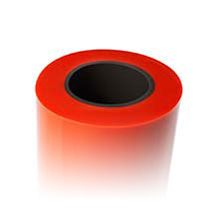
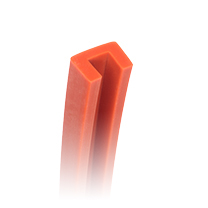
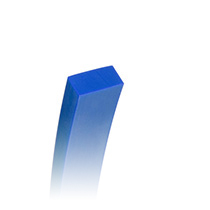
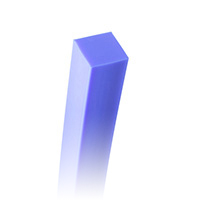